Fighting COVID-19: Printing Face Shields for Local Hospitals
- Chloe W.
- May 7, 2020
- 2 min read
When I was first contacted by Chloe Wang about an opportunity to 3D print face shield parts for frontline workers, I immediately wanted to jump in.
Our club had just recently bought and built a Prusa i3 MK3S 3D printer to use for the club along with a new spool of PETG filament. We had decided to keep the 3D printer at my house, so we could print and manage it more before the crisis. We were lucky in this decision as school would be closed weeks later for an uncertain amount of time, where students were not allowed on campus.
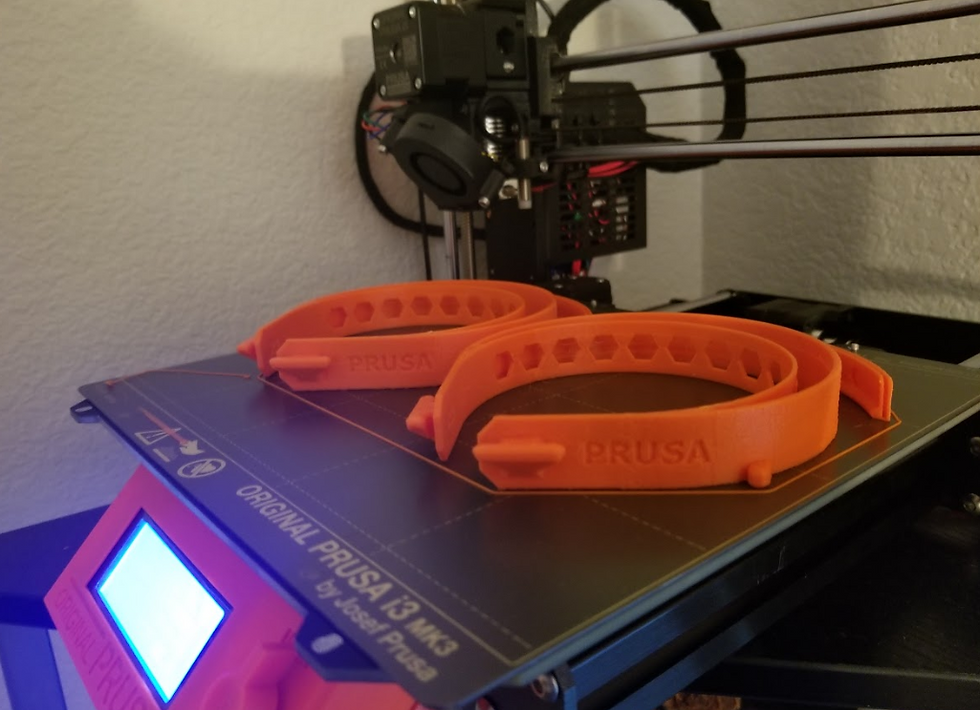
I was then able to set up the printer in my room, and to my computer. After fixing issues with the belt system, it was ready to print after numerous failed prints. The prints were gorgeous, were able to overcome printing challenges, and had a very fast print time. With this knowledge, I knew our printer would be able to print face shield parts.
The design we had been told to print was the Prusa Face Shield that had been made by Prusa Research as a response to COVID-19. Our job was to print the top headband and the bottom reinforcements, but we still needed the clear plastic visor for each mask.

The people that had contacted us were working with a Makerspace called MakerNexus that would make the visors and assemble the mask. With that knowledge, I had begun printing and following the instructions they had given us.
To make sure that the 3D printed pieces would not get contaminated, we were told to put them in plastic bags with only five pieces in each to avoid cross contamination. A volunteer driver would then be able to pick up my parts and deliver them to MakerNexus.
PETG filament was preferred for the parts as it is more flexible and it is easier to disinfect. I used our new spool of orange PETG to print, and the first parts came out well. Due to how early we got involved, the design was constantly being optimized and we were having to keep up with the constant changes in how to print it more efficiently.

The printing process was going well and everything was going according to plan. The people we were working with were even able to give us two new spools of filament after we had run out.
MakerNexus was then able to optimize their process even more by injection molding the headband parts of the face shields. They are now able to make an outstanding 6,000 headbands per day. Due to this, we had been told to focus on only making bottom reinforcements.
More students of our club are even beginning to get involved by using either their personal printer or a friend's printer, and I could not be more excited to see how many parts we end up printing.
Today, I have printed a total of 44 headband parts and 153 bottom reinforcements that have already been delivered to MakerNexus. I could not be more grateful to MakerNexus for allowing me to be a part of their COVID-19 reponse and Chloe Wang for letting me know of this opportunity to help.
Written by Nick Azpeitia (2019-2021 CAD Manager and 2020-2021 Co-Vice President)
Comments